Serafín Tortosa, el maestro imborrable que sigue formando el futuro de la cerámica
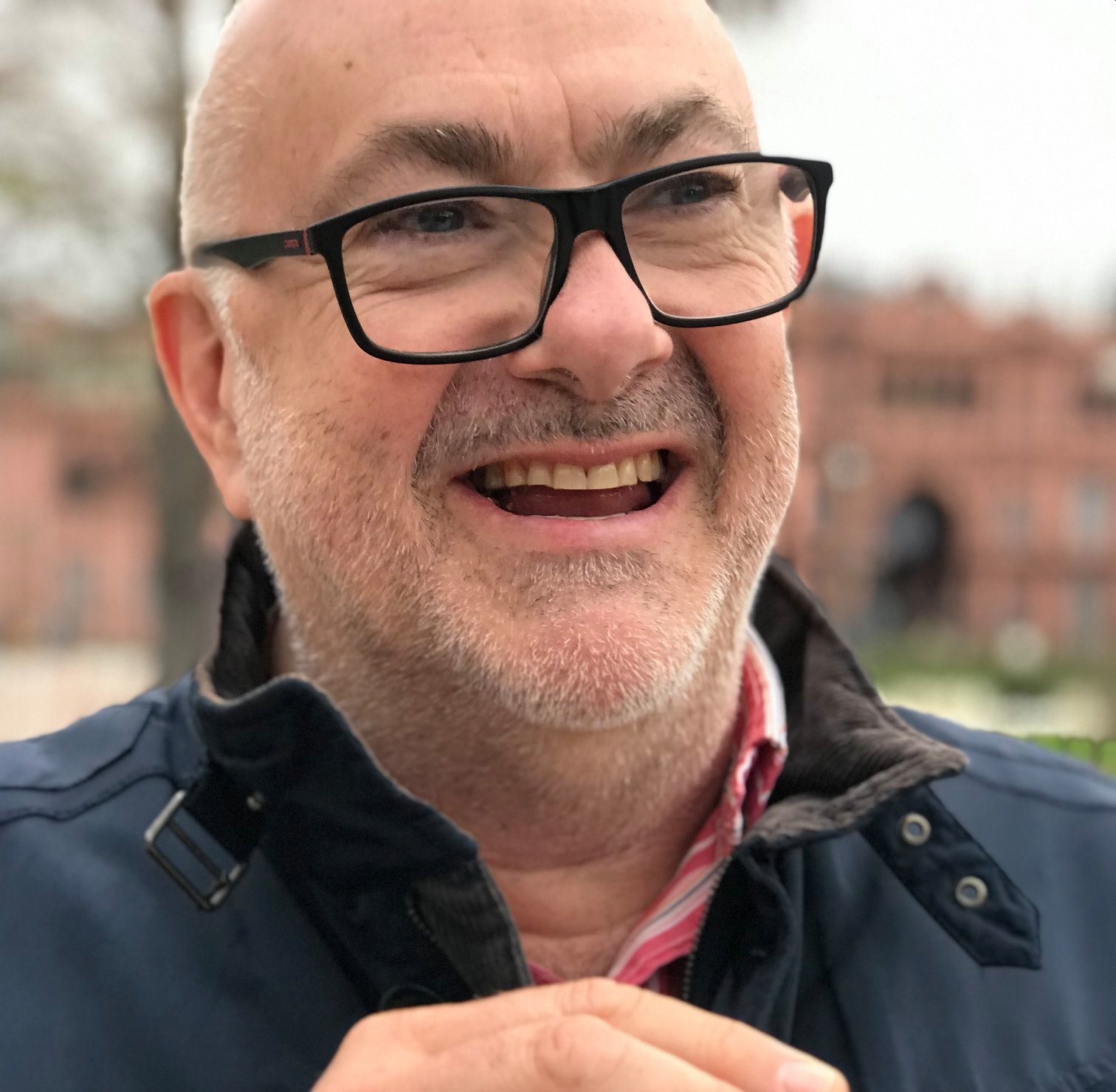
ATC quería formar a los técnicos y difundir los conocimentos entre todos nosotros
Parece que usted estaba predestinado a trabajar en el ámbito cerámico.
Sí, nací arriba de una alfarería. Mi madre tenía una alfarería que llevaba mi padre como técnico, de hecho fue el primer técnico que yo conocí. Y después fue mi hermano el que llevó también la dirección de la alfarería hasta que se cerró en 1998.
Yo quería estudiar Económicas, pero las circunstancias se presentaron de esta manera y me encontré estudiando en la Escuela de Cerámica de Manises. Después me fui a Peronda y tuve que dejar Económicas porque era incompatible trabajar en Peronda, en Onda, e ir a estudiar a Valencia.
¿Y cómo llegó usted a Peronda?
Resulta que Joaquín Perís, el que ha sido mi jefe y compañero durante todos estos años, hizo el servicio militar en Manises y, durante ese periodo, iba a la Escuela de Cerámica. Él solicitó a la Escuela de Cerámica que enviaran un alumno para trabajar en Peronda y me enviaron a mí.
Fui el primer técnico de Peronda, porque entonces el único técnico que había era el propio Joaquín, que era dueño, director de fábrica, director gerente, financiero… Yo fui ayudándole y, poco a poco, pasaron 48 años de trabajo.
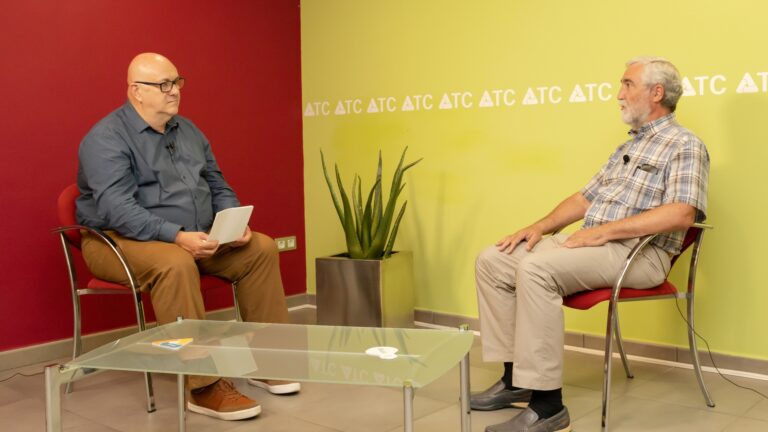
¿Y qué funciones desempeñó hasta llegar a Director Técnico de Producción?
En realidad siempre he tenido el mismo puesto de trabajo. Joaquín Peris era el director y yo estaba en la parte técnica. Después entró Ángel Olmos, que antes había trabajado en Colorificio Cerámico Bonet; y otro compañero, Ricardo Marín, que estaba en La Nao, que era una fábrica de Onda. Los tres compartíamos piso cuando éramos solteros.
¿Con qué fábrica se encontró cuando llegó a Peronda en 1973?
Había muchísimas cosas que se hacían de forma manual. Se plegaban las piezas en la prensa. A la salida de la prensa había un acarrillador, pero el plegado y la carga de las vagonetas era a mano. Las prensas eran de fricción, no eran prensas hidráulicas como las actuales. Había siete prensas, de las cuales 5 eran de Fatmi de 175 toneladas que podían prensar o que decían que podían prensar hasta esa fuerza, pero aquello era un tornillo que daba vueltas y que aplicaba presión, pero no se podía controlar la presión que aquello hacía sobre las piezas. Una prensa 220 y una 500 también de fricción. La molienda era con molinos de barrotes en vía seca, no había todavía atomizadores ni nada por el estilo.
Todo era vía seca y todo el movimiento de las arcillas era semiautomático o el movimiento de las vagonetas era por vías y todo manual… Horno túnel, secadero túnel, presecadero anteriormente… ciclo como mínimo de casi una semana… Tú hacías una maniobra en la prensa y hasta el cabo de 4 o 5 días no podías saber el resultado. La clasificación del bizcocho también se hacía a mano, se llamaba espolsar, al igual que alimentar las máquinas de esmaltar. Los formatos que hacíamos eran muy pequeños: los tacos de 11×11 o los cuadronets de 15×15 centímetros. Eran formatos que el albañil, con una mano, podía coger la pieza.
¿Ya se comparaba a la industria española con la italiana?
Sí, pero Italia era… era otro mundo. Tardamos, por lo menos, 20 años en alcanzarles, incluso después superarles. Las máquinas eran las mismas que teníamos nosotros, pero nos llevaban ventaja en cuanto a diseño y en su capacidad para vender el material. Después, poco a poco, se fue recortando esa diferencia.
Ahora estamos equiparados porque hay fábricas italianas que producen muy bien el producto y el diseño, y también hay fábricas españolas que están a la cabeza mundial en cuanto a la calidad, diseño y formatos. No hay una gran diferencia. Desgraciadamente, tampoco existe esa diferencia con respecto a otros países del mundo.
¿Qué motivos se dieron para que España avanzara tan rápidamente en aquellos años?
La maquinaria, casi siempre, ha venido de los italianos, y ellos no privilegiaron a sus fábricas, sino que la vendieron a todo el mundo. Eso nos permitió igualarnos bastante. Yo llegué a Peronda en 1973, y en el año 1983 montamos el primer horno monoestrato, y ya habíamos montado prensas hidráulicas: una 555 primero, una 650 después. Yo cuento muchas veces que en Peronda hemos derribado y vuelto a construir la fábrica tres o cuatro veces. Por dentro no hay nada que sea la original. Por un lado la maquinaria ha influido mucho, cuando entró el monoestrato fue una revolución y cuando entraron las prensas hidráulicas fue otra revolución. Yo creo que esas dos innovaciones han sido fundamentales.
El último cambio que hemos vivido, ya no procedente solo de Italia, sino que ya España en ese aspecto ha sido pionera, ha sido la inyección. Las máquinas de inyección están revolucionando todavía más si cabe la forma de fábrica de azulejos y la variedad de tonos. En una serigrafía todas las piezas eran iguales, en una inyección las piezas pueden ser todas diferentes y podemos imitar la naturaleza de una manera extraordinaria.
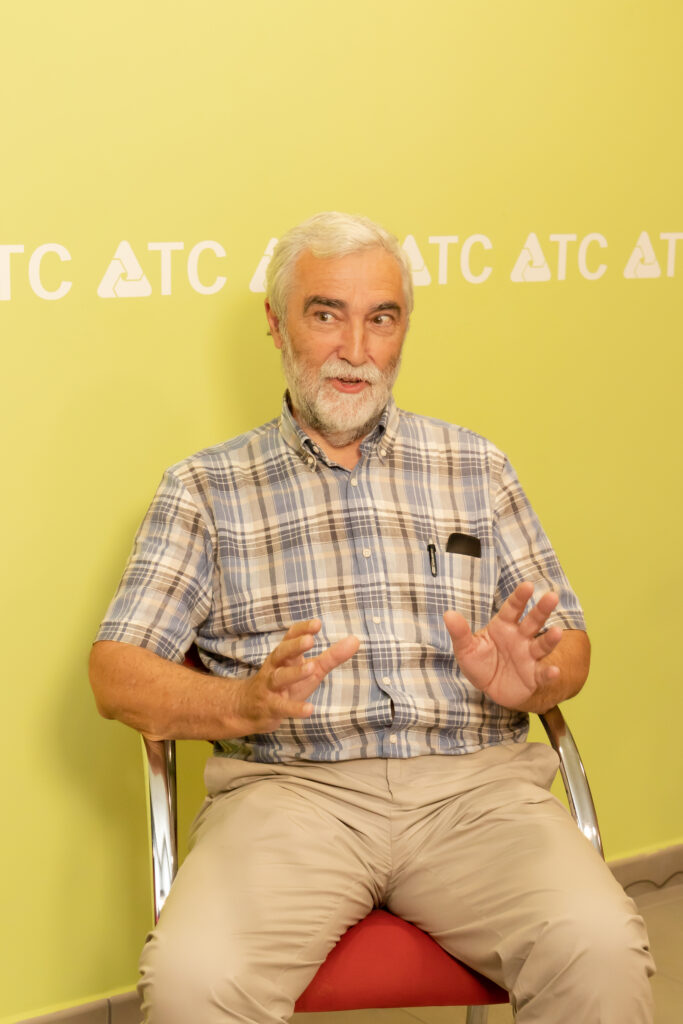
¿Qué motivos se dieron para que España avanzara tan rápidamente en aquellos años?
La maquinaria, casi siempre, ha venido de los italianos, y ellos no privilegiaron a sus fábricas, sino que la vendieron a todo el mundo. Eso nos permitió igualarnos bastante. Yo llegué a Peronda en 1973, y en el año 1983 montamos el primer horno monoestrato, y ya habíamos montado prensas hidráulicas: una 555 primero, una 650 después. Yo cuento muchas veces que en Peronda hemos derribado y vuelto a construir la fábrica tres o cuatro veces. Por dentro no hay nada que sea la original. Por un lado la maquinaria ha influido mucho, cuando entró el monoestrato fue una revolución y cuando entraron las prensas hidráulicas fue otra revolución.
Yo creo que esas dos innovaciones han sido fundamentales.
El último cambio que hemos vivido, ya no procedente solo de Italia, sino que ya España en ese aspecto ha sido pionera, ha sido la inyección. Las máquinas de inyección están revolucionando todavía más si cabe la forma de fábrica de azulejos y la variedad de tonos. En una serigrafía todas las piezas eran iguales, en una inyección las piezas pueden ser todas diferentes y podemos imitar la naturaleza de una manera extraordinaria.
Tres años después de ingresar usted en Peronda se funda ATC…
Juanjo Martínez, del laboratorio Sebastián Carpi, fue, en alguna medida, el que aglutinó a un grupo de técnicos, algunos de Onda, algunos de Alcora y algunos de Castellón o de otras partes de la zona… Fue el que promovió aquello y, de hecho, las primeras reuniones las hicimos en el Laboratorio Sebastián Carpi. Yo creo que ese fue el núcleo de por qué surgió la Asociación de Técnicos Cerámicos.
Todos conocíamos a Juanjo porque le llevamos los análisis, las muestras de arcilla o de lo que fuera para poder ir aprendiendo alguna cosa. Y entonces, a partir de ahí, él fue convocando a todos… De hecho, él fue al final el primer presidente de ATC. Yo creo que le debemos mucho a Juanjo porque fue, en ese aspecto, una persona extraordinaria para la Asociación de Técnicos Cerámicos y para todo el sector.
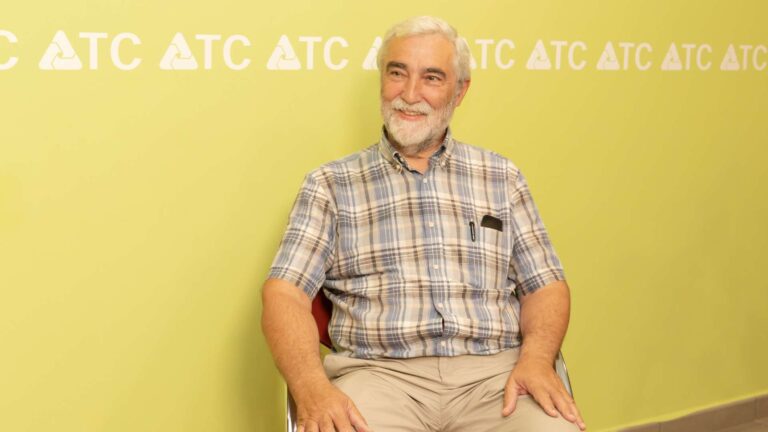
¿Pero qué objetivos se querían lograr?
Yo creo que lo que se quería conseguir, fundamentalmente, era formar a los técnicos. Difundir entre todos nosotros los conocimientos. Yo, de hecho, di un salto cualitativo gracias a ATC, porque en la Escuela de Cerámica había estudiado Cerámica, pero cerámica artística, cerámica de Manises. No había visto nunca una fábrica de azulejos, ni era similar a lo que estudiábamos allí. En la ATC hicimos un curso de 6 meses, que íbamos dos tardes a la semana al Colegio de Ingenieros Industriales. Cada tarde íbamos a escuchar a un profesor diferente que daba una charla sobre lo que él conocía. Por ejemplo, me acuerdo que de molienda vino Bono, el de Jois Benassi; también vino José Emilio Enrique Navarro, que era entonces de la Facultad de Químicas de Valencia, y el profesor Escardino. Quien también dio una charla fue el ingeniero Poppi, que era el que construía los hornos túnel que comercializaba Sacmi.
¿Cuáles eran las prioridades del sector en aquellos años 70?
El medio ambiente ni se conocía. Sí que intentábamos mejorar la calidad, pero fundamentalmente por la rentabilidad, claro. No es lo mismo vender primera que vender segunda, aunque entonces la segunda tenía buen precio. Nosotros entonces hacíamos primera, que era la estándar; la segunda, que era la comercial, la tercera y la cuarta, y los rotos. Había 4 calidades. Y los rebucheros estaban esperando a que los clasificadores terminaran su trabajo para llevarse las clases
bajas porque después ellos las reclasificaban o directamente, sin reclasificar, le ponía el cuño de primera y las vendían como podían. Tampoco el público exigía unas calidades extraordinarias. En el bizcocho no había segundas y terceras. Ese bizcocho o era bueno o era basura. Con lo cual, mejorar el bizcocho sí que fue muy importante, porque si no lo hacías de calidad, el bizcocho era rotura y entonces no podías esmaltar el material y te faltaba producción para el horno de fino.
¿Y a nivel energético?
En los primeros años, nosotros gastábamos fuel. No teníamos gas natural, ni gas propano. Después en el horno de fino se pusieron unas lanzas con gas propano y después ya vino el gaseoducto. Nosotros todavía llegamos a hacer toda la transformación del fuel a gas propano. Nuestro segundo horno túnel ya nació con gas propano. Teníamos un depósito grande de propano y la cuba venía cada dos o tres días. Después ya, cuando vino el gaseoducto, llegaron los hornos monoestrato y el gas natural. Cada vez hemos ido a hornos más grandes, a hornos de más producción… Y cuando aumentas la producción, el consumo suele descender, con lo cual siempre estamos reduciendo el consumo. Después se han hecho ya transformaciones de quemadores más eficientes, de hornos más eficientes cada vez, más aislados.
También secaderos con mayor efectividad. Contamos con higrómetros que miden la humedad en la chimenea de los secaderos, medimos la humedad a la que sacamos las piezas. Intentamos no tirar aire al exterior que lleve poca humedad. Es aire caliente que en realidad lo estamos tirando en balde al exterior con lo cual, cada vez tenemos recuperaciones del horno, con intercambiadores tanto de aceite como de aire. Todo eso es una evolución. Yo tengo una presentación con más de 100 acciones de ahorro energético que se pueden hacer en una fábrica, no solo de gas, sino también de electricidad, de mejora de las maquinarias, de aumento de la producción… Mejoras que al final también es eso, ahorro energético.
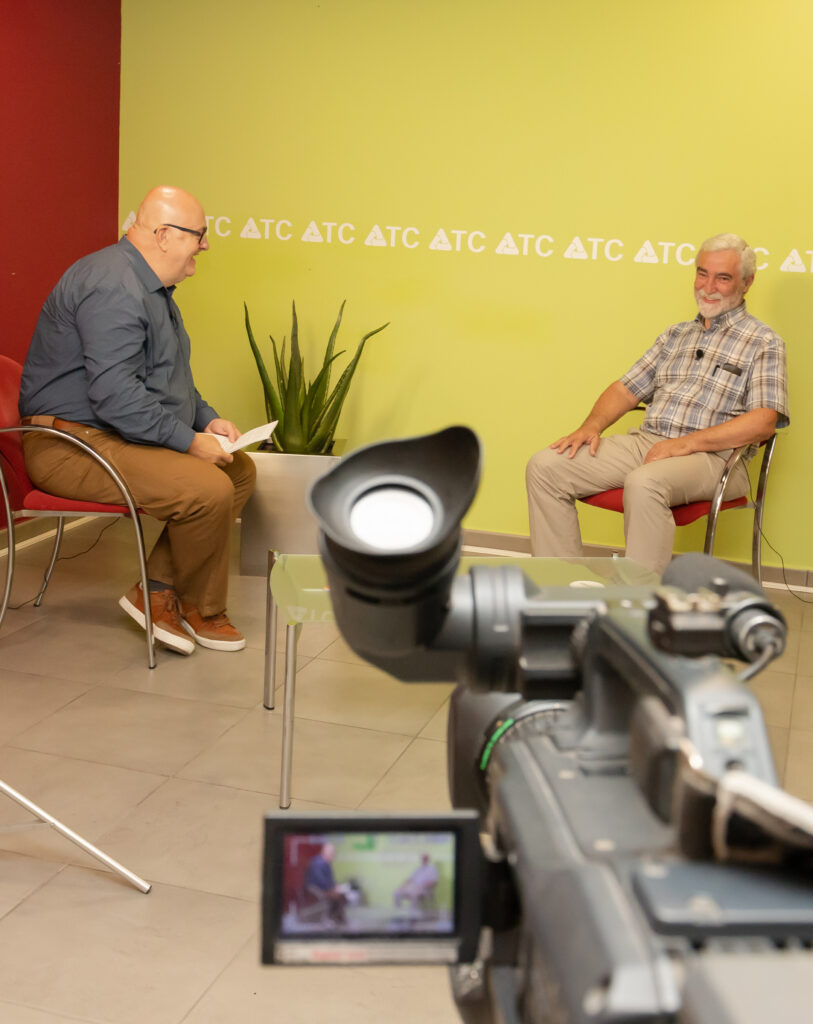
¿Considera que la especialización es negativa? ¿Apuesta por un técnico más multidisciplinar?
Sí, porque la división del trabajo… llega un momento en que nadie en la fábrica tiene una visión global, y esa es una gran ventaja que he tenido, porque me ha dado una visión global de toda la fábrica. Mientras que muchas veces los técnicos… uno está en las prensas, otro está en el pintador, otro está en el horno, otro esta… o no se comunican mucho entre ellos. A veces compiten… Yo he estado en fábricas donde el bizcocho se lo vendían a los de la esmaltadora… No he trabajado yo en esa fábrica, pero he conocido fábricas donde se lo vendían. Claro, el del bizcocho qué quería, que todo fuera bueno. El de la esmaltadora, qué quería… “como esté un poquito tostadito ya te lo comerás tú, que yo no lo quiero. ¿Por qué? Porque si me sale a mi mal y me quita mi calidad… Y si te rechazo el bizcocho, yo estoy mejorando mi calidad, pero tú estás empeorando tu calidad”. Esa competencia yo no la quiero… Yo he tenido la ventaja de que he estado siempre a nivel global en la fábrica y muchas veces resuelves problemas, porque sabes lo que está pasando en prensas y lo que está pasando en el horno, que a veces tiene que comunicarse para ver si hay… No, a veces, no, siempre hay que comunicarse para… Y esa buena comunicación, esa buena relación hay que regarla, hay que abonarla y hay que fomentarla… Comunicar es muy difícil y comunicar bien, es mucho más difícil todavía. Y comunicar en dos sentidos, tanto para arriba como horizontalmente, es muy complicado y a veces se nota esa falta de comunicación. Entonces, por un lado es bueno que el técnico se especialice, pero también es bueno que haya por lo menos algunos técnicos que tengan un conocimiento global de lo que es la producción, no se queden solo en su zona.
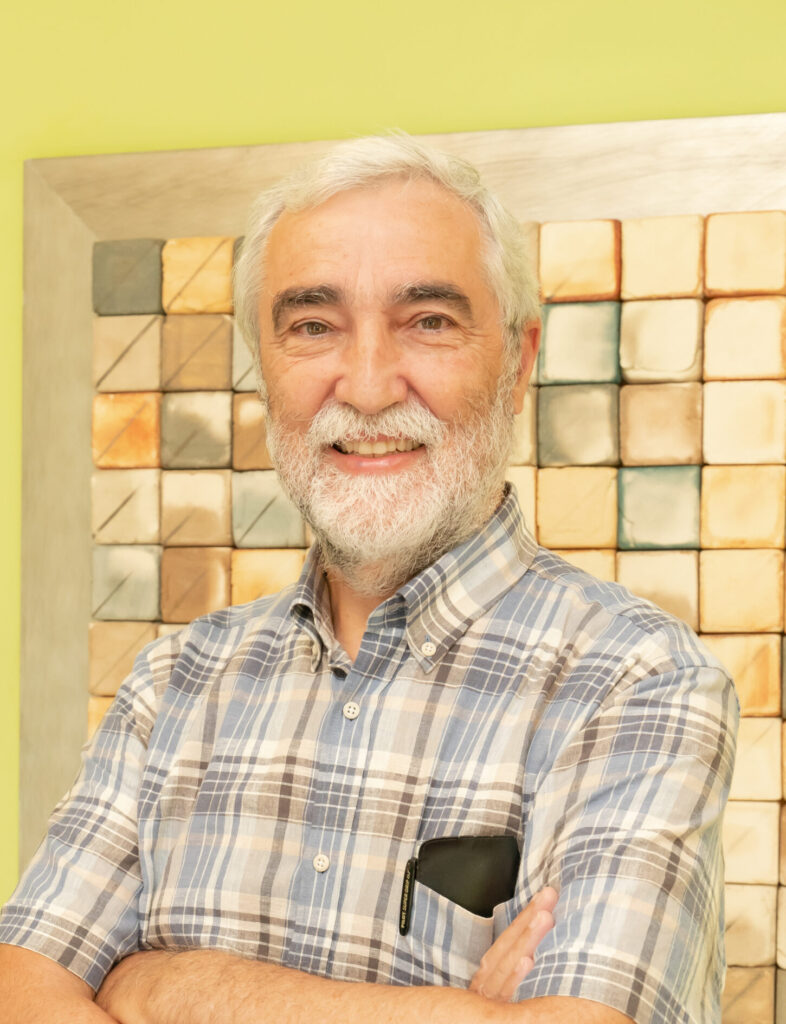
Porque el técnico tiene que estar siempre en constante formación…
Por supuesto. Yo lo decía, he hecho cinco carreras en toda mi vida. ¿Por qué? Pues porque yo he hecho cursos de informática, he hecho cursos de inglés, de italiano, de MS2, de prensas… O sea, yo he hecho cursos de todo. Di el tema que quieras y de eso he hecho cursos.
¿Precisamente, su apuesta por la transferencia del conocimiento le llevo recibir en 2017 la insignia de oro de ATC.
Bueno, eso fue el culmen de mi carrera. Yo estoy muy agradecido a ATC. He dado mucho a ATC, pero también he recibido mucho de ATC. He recibido mucha formación al principio, y después he sido yo el que la ha impartido… A mí hay mucha gente que me conoce en el sector, y que yo no sé quiénes son. Y me conocen porque he aparecido en la revista Técnica Cerámica con algún artículo o porque me han escuchado en alguna conferencia de ATC… El espíritu de ATC es ese, es compartir, es dialogar.