Tradición y vanguardia: explorando la evolución cerámica de la mano de Luis Hernández
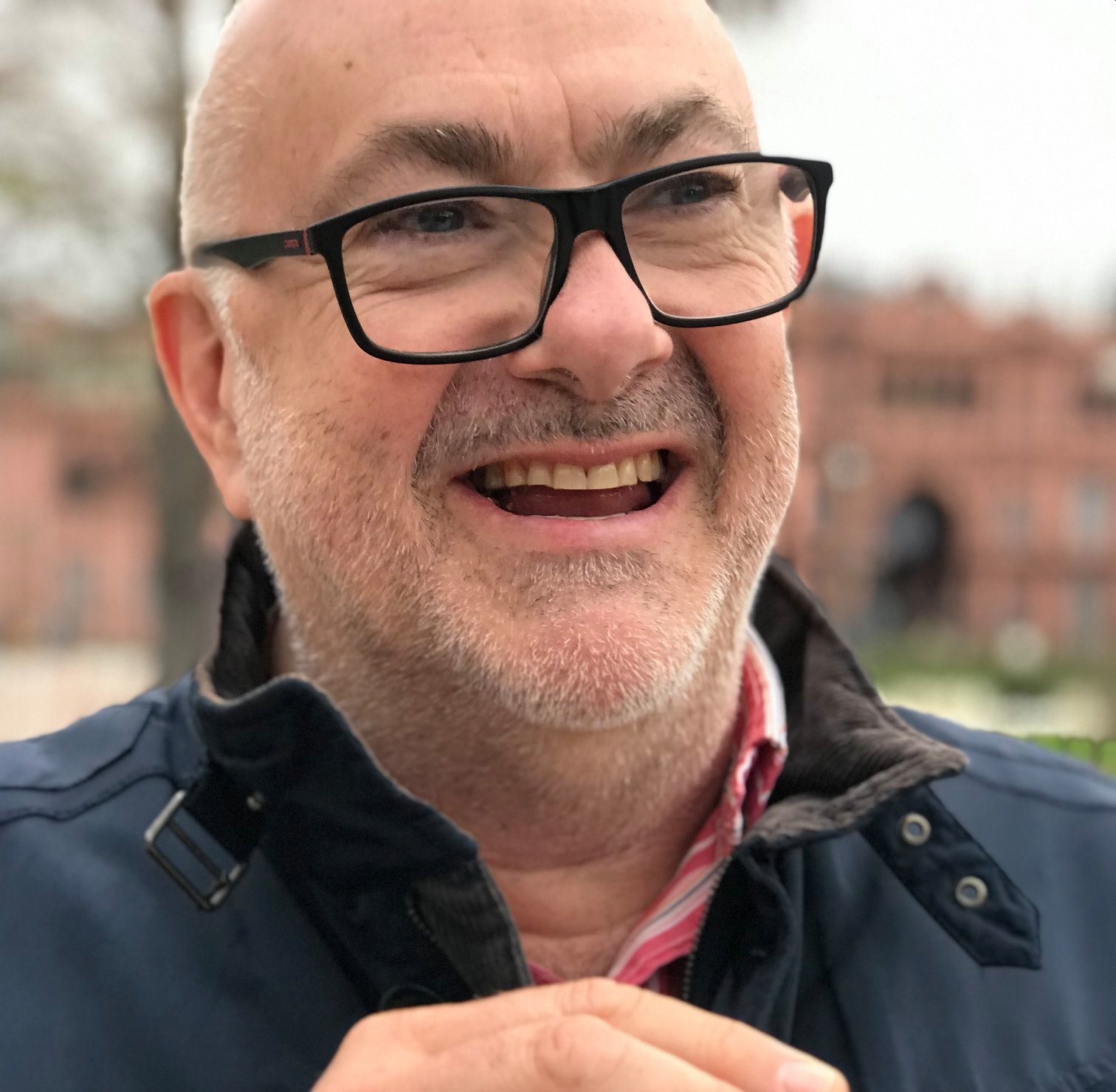
Las empresas de España son más productivas que las italianas.
Usted es heredero de una rica tradición familiar en el sector cerámico…
Tener una tradición familiar impone unas obligaciones. Mi bisabuelo fue el creador de la primera empresa de azulejos en l’Alcora, fue alcalde de la ciudad; a él le sucedió mi abuelo, que fundó Azulejos Sanchís a principios del siglo XX y, posteriormente, mi padre y mi tío, José Hernández Cañizares y Vicente Sanchís.
Fueron muy emprendedores y crearon Inca, una industria importante en aquel tiempo, fundaron Esmaltes y continuaron por supuesto con la actividad de Azulejos Sanchís. Grespania fue una nueva creación, que surgió en 1976 como una empresa nueva, pero con una carga familiar importante.
Sin embargo, usted empezó a trabajar en una empresa de automatización y, luego, en la banca industrial.
Viví bastante lo que era la industria cerámica de niño porque mi padre tenía la costumbre de que el primer día de vacaciones había que pasarlo en la fábrica y a mí, la fábrica, me parecía atractiva, incluso un sitio de jugar, de aprender, de conocer gente… Se aprendía mucho hablando con los trabajadores y de los encargados de aquella época. Estudié Ingeniería Industrial en Madrid y, cuando acabé, entré a trabajar en la Siemens, en una actividad muy innovadora en ese momento, que era la automatización de procesos industriales mediante ordenadores. Trabajé durante año y medio pero en realidad lo que me atraía era la parte financiera de la industria, lo que me llevó a trabajar en la Corporación Industrial del Banco Urquijo durante cinco años.
Probablemente no hubiera llegado al sector cerámico, si mi padre no hubiera tenido un proyecto de inversión. Quería que le ayudase en el estudio de creación de una fábrica nueva, porque Azulejos Sanchís estaba muy constreñida dentro del pueblo de l’Alcora y, entonces lo que parecía que iba a ser una ampliación en la que yo iba a colaborar con una asesoría técnica como ingeniero, vi que era un negocio interesante. Pensé que había que darle un giro más moderno a una industria de ese tipo y de ahí surgió la creación de Grespania fuera del ámbito de l’Alcora, ya en Castellón, y con un concepto de futuro más pensado en la exportación, basada en productos más actuales.
Grespania nació con un concepto de futuro basado en la exportación"
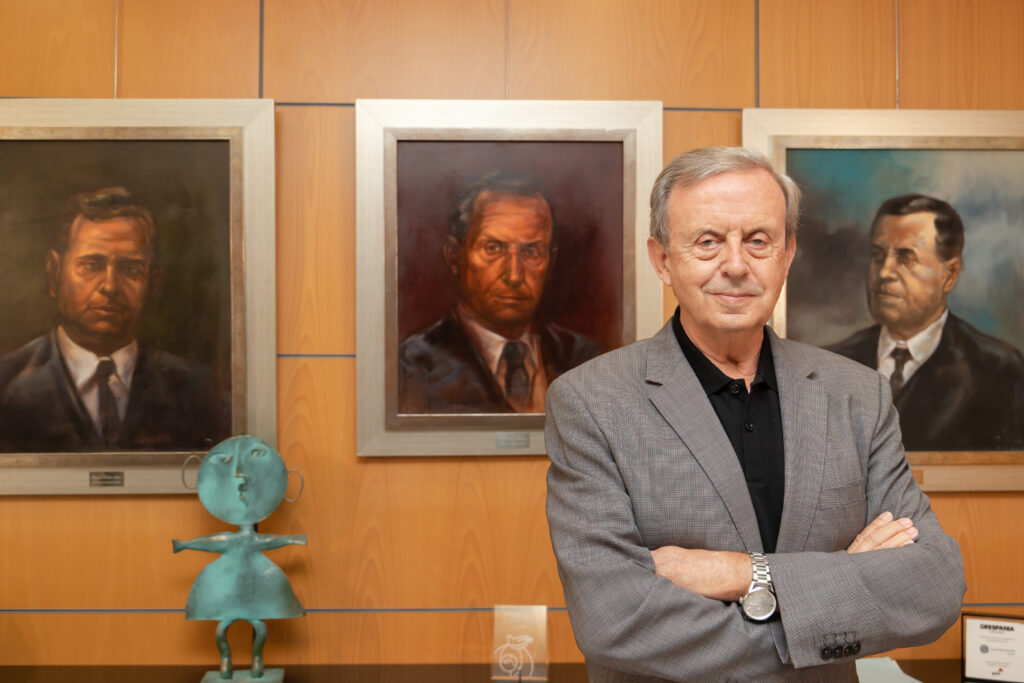
¿Qué aportó Grespania? ¿Qué la diferenciaba del resto de empresas en aquel momento?
Nos preocupamos mucho por el diseño de los productos. Muy pronto creamos un departamento de diseño y también apostamos por la relación directa con la exportación. En aquel momento, las empresas no tenían capacidad para tener sus propios departamentos dedicados al comercio exterior, salvo alguna excepción. Se agrupaban en unidades de exportación tanto por temas fiscales como operativos y, a lo mejor, en una de esas unidades había agrupadas ocho o nueve empresas.
Yo pensé que aquello no podía ser así, sino que debía de tener un carácter diferenciador en su producto. Debía tener un control directo por parte de la empresa de lo que eran las ventas internacionales. Yo creo que esas dos cosas son lo que principalmente aportó Grespania en sus inicios, una actividad exportadora propia y una gestión propia de lo que era el diseño y el desarrollo del producto.
A nivel tecnológico, ¿Cómo estaban las fábricas españolas?
A nivel tecnológico, algunas fábricas españolas habían hecho una cierta revolución industrial. A partir de los años 60, España introduce ya hornos túneles. Cuando yo llegué a este sector muchos no los tenían, había muchos hornos bicanales, había hornos de pasajes, hornos árabes… pero ya se había iniciado un
poco la modernización de las fábricas con la implantación de los hornos túneles y con las prensas de fricción, pero estaban ya controladas electrónicamente. Estos eran los avances que España había introducido a partir de los años 60 pero aún el sector, tecnológicamente, estaba algo más atrasado que la industria italiana.
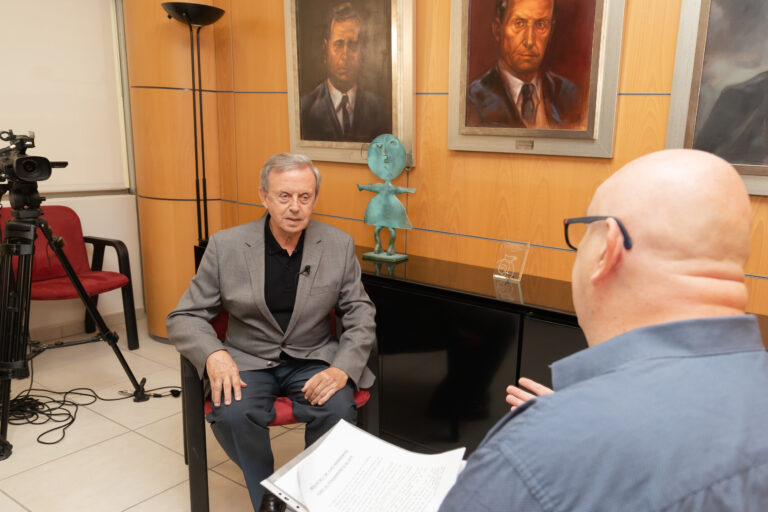
La invención de la monococción fue un hito importantísimo para España, ¿Qué supuso?
Sí, la introducción de la monococción, muy a principios de los años 80, supuso una automatización mayor de la cocción y, sobre todo, poder fabricar algún tipo de producto que, hasta ese momento no se podía producir o se hacía con muchas dificultades técnicas. Supuso la modernización de las fábricas y los españoles fuimos pioneros en adaptar este sistema al proceso de fabricación del revestimiento. Por lo tanto, aunque fue un invento italiano, la monococción porosa fue una innovación española.
¿Cuál era la situación del equipo humano del sector cerámico en aquel momento?
A mediados de los 70 ya se había iniciado una tecnificación de las empresas. Era un panorama distinto al que había conocido de niño en la fábrica de mi padre y mi tío. En los años 50 y mediados de los 60, las fábricas estaban en manos de los encargados, figura valiosa con una dedicación notable a las empresas, que tenían un conocimiento práctico de la cerámica, pero faltaba el bagaje técnico, por ejemplo, en la creatividad del producto, el diseño de las plantas…
que es lo que aportaron luego los técnicos cerámicos. A mediados de los 60 se había producido en algunas fábricas importantes la entrada de ingenieros técnicos, peritos como se llamaban en aquella época, y también ingenieros industriales y químicos. Pero eso todavía no estaba consolidado. Cuando yo llegué al sector empezaban a entrar en las fábricas de forma masiva ingenieros y químicos. Era ya una tendencia irrefrenable.
Además de la monococción porosa ¿Qué otros acontecimientos han sido importantes en la evolución del sector en la segunda mitad del siglo XX?
Hay cuestiones, como la incorporación de tecnologías, que han supuesto una revolución fuerte en el sector y hay otras que han sido importantes aportaciones españolas a esa revolución tecnológica. Entre otras, la introducción del horno túnel. Cuando llegué al sector estaba en ciernes otra revolución importante, que fue la introducción de los hornos de rodillo de cocción rápida, que supuso un cambio fortísimo mediante unas inversiones muy importantes, ya que hubo que abandonar totalmente la tecnología anterior. Este cambio vino casi unido a la llegada de las prensas hidráulicas que se produjo un poco después y que permitió hacer piezas de mayor tamaño, evitando muchos defectos de producción. Y, por supuesto, la otra revolución tecnológica importante fue la inyección digital que cambió no solo la forma de decorar los azulejos, sino que permitió hacer
productos que, hasta entonces, eran muy difíciles de hacer y también influyó mucho sobre lo que era el proceso de diseño de los azulejos.
Finalmente, yo creo que el último hito importante, pero que para mí no supuso una revolución tan fuerte como las que he nombrado, ha sido la fabricación de las piezas de gran tamaño. Hay que pensar que, por ejemplo, cuando llegué a esta industria, las piezas de mayor tamaño que se fabricaban eran de 10×20 y de 20×20 centímetros, y hoy en día se hacen piezas de 120×360 centímetros. La fabricación de láminas de gran tamaño en la industria cerámica nos ha liberado de ese corsé que era el tamaño del azulejo.
Todas esas innovaciones tecnológicas las incorporó usted a Grespania, incluidos los grandes formatos con la creación de la marca Coverlam para fabricar en continuo…
El concepto de la pieza de gran tamaño es algo que, a nivel tecnológico, surgió a principios de la primera década de los años 2000. Durante mucho tiempo fue una curiosidad tecnológica que nadie llevó a la práctica pero pensé que era algo interesante porque abría nuevos campos a la cerámica. Y es que permitía usos como la fabricación de muebles, encimeras para cocinas, revestimiento de fachadas de edificios singulares…
En definitiva, ampliaba el mercado tradicional de los productos cerámicos. También estoy convencido de que se trata de un tipo de producto más en el mercado cerámico y que no va a desplazar a los azulejos tradicionales, pero va a abrir un campo adicional de trabajo en cierto tipo de construcción y en la fabricación de otros materiales.
Antes de Coverlam usted puso en marcha otros proyectos como es Kerlux y nuevos productos cerámicos, ¿Cómo surgieron y qué han aportado?
Como he comentado, lo primero que hicimos fue la instalación de una planta de fabricación por monococción de gres por vía seca que, además, era otra innovación porque todo el mundo hacía este tipo de productos con polvo atomizado. Luego, en el año 1986, montamos una planta de fabricación de azulejos de revestimiento por el proceso de monococción porosa en pasta blanca que, en su momento, tenía cierta carga innovadora aunque algunas industrias lo hacían, pero la novedad de aquella planta que hicimos en Nules era que la construimos bajo un concepto de vertido cero: todo era reciclado, cosa que en aquella época era bastante innovadora. Reciclábamos las aguas sucias que venían de la esmaltadora, todo el azulejo roto en esmaltadoras, el polvo de los filtros… Es decir, no vertíamos nada al exterior. Y eso fue muy innovador, incluso hoy en día es común en el sector que los atomizadores reciclen los lodos de
esmaltadoras o el azulejo desechado pero en aquella época fuimos los primeros que lo hicimos.
Luego, en 1996 montamos Kerlux, que era una empresa dedicada al azulejo de pequeño tamaño, también a todo tipo de decoración, sea monococción o sea tercer fuego, listelos… Esta fue una empresa que después absorbió Grespania. Años después, al principio de 2000 y junto a otros empresarios del sector, fundamos Nuevos Productos Cerámicos, una firma de atomización importante que se dedicaba a pastas atomizadas de todo tipo, siempre en pasta blanca, y posteriormente absorbió a uno de sus principales competidores, Euroatomizado. Finalmente, en 2016, fue cuando montamos la planta de Coverlam para la fabricación de piezas de gran tamaño.
La introducción de la pasta blanca también fue una innovación para el sector español. Se dice que fue una imposición de Italia para quitarnos las ventajas que teníamos con la pasta roja, ¿Fue realmente así?
Yo creo que no fue exactamente así. Es una realidad que para fabricar porcelánico hay que recurrir a las pastas blancas, y en España. Históricamente había algunas empresas que, en el campo del revestimiento, producían con estas arcillas, pero no en la provincia de Castellón, sino en Burgos y en la provincia de Guadalajara. Antes de la llegada del gres porcelánico, la fabricación de azulejos de este tipo, tanto revestimiento como pavimento, estaba solo en manos de tres o cuatro empresas. Entonces, sí que era un proceso innovador.
En ese momento, la mayoría de pavimento y revestimiento que se hacía en España era de pasta roja. España es muy abundante en arcillas rojas locales, que están muy cerca y son muy baratas, pero con las cuales, hoy en día, ciertos productos no los podemos fabricar. Pavimentos o revestimientos de gran tamaño o el pavimento porcelánico no se pueden hacer con las características adecuadas y con la confianza de calidad que nos da la pasta blanca. Derivar hacia este tipo de arcilla ha sido una necesidad de producto.
ATC le entregó a usted su máxima distinción, la insignia de oro, en 2017 por su aportación a la evolución del sector cerámico. ¿Qué significó para usted ese premio?
Para mí fue un gran honor porque, aunque soy empresario, me considero técnico y que le reconozcan a uno como ingeniero cuando realmente es empresario y en el fondo de su corazón se siente tanto ingeniero como empresario… La verdad es que lo agradecí enormemente.
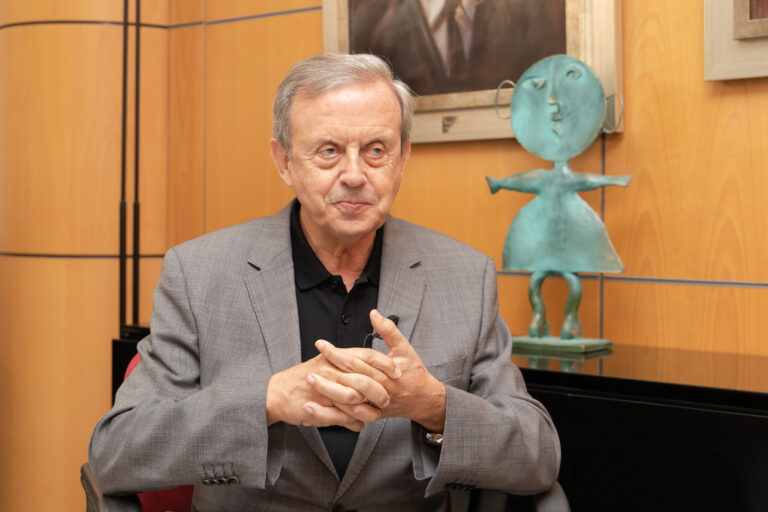
Ahora mismo podemos decir que casi todos los países producen cerámica ¿Qué papel juega en la actualidad nuestro país en esta situación?
En la actualidad, España se ha puesto al mismo nivel de diseño y de calidad que Italia e incluso la supera. Hay un campo en el que nuestra industria está por delante, y es el de la productividad. Hoy en día, las empresas españolas son más productivas que las italianas, están tecnológicamente mejor dotadas y el concepto de reducción de costes y de productividad es, para mí, más alto en nuestro país.
Pero Italia sigue teniendo una imagen superior como país y, especialmente, como diseño, y además sus comerciales son más hábiles en el manejo de los mercados, campo en el que, en este momento, nos supera, aunque esa diferencia se está reduciendo.
¿Qué recuerdo destacaría usted de toda su trayectoria profesional?
Para mí fue muy importante cuando inicié la producción del gres de monococción por vía seca. Recuerdo que hicimos unas pruebas en una planta piloto italiana en la que participé junto a otros técnicos. Estuvimos produciendo dos días hasta que vimos que aquello, realmente, se podía fabricar.
Fue un invento. También recuerdo con especial cariño cuando pusimos en marcha la fábrica de producción de azulejos de pasta blanca con el tema de reciclado, que también fue un invento nuestro.
¿Cuáles son las personas que más le han influido en su trayectoria en el sector cerámico?
Encontré empresarios de la generación de mi padre que, realmente, me parecieron muy capaces, muy serios, con un gran sentido de la responsabilidad. Por supuesto, citaré a mi padre, José Hernández Cañizares, que era un magnífico administrador; y a mi tío, Vicente Sanchís, una persona muy creativa y emprendedora. Pepe Soriano era una persona genial en sus conceptos comerciales de producto, y ahí está todo lo que él hizo.
José María Valls, que fundó Azul Valls y Gres de Valls, era una persona creativa, seria… Juan Pitarch, que llevaba Zirconio, también era una persona de ese mismo estilo y fue presidente de Ascer; Miguel Carda, que también presidió Ascer, era un hombre culto y sensato… Fueron empresarios que aportaron una fibra y un dinamismo al sector cerámico importantísimos. Hicieron que las empresas fueran confiables para la banca, para la administración, para los mercados exteriores.