Ventajas del uso de la tecnología de rayos X en el control de calidad de la fabricación de baldosas cerámicas.
Medida de la densidad de materiales por rayos X
La tecnología de absorción de rayos X nos permite determinar la distribución de la densidad aparente en el interior de los materiales, de forma no destructiva, no perjudicial para la salud y respetuosa con el medio ambiente. Por esta razón, es ampliamente utilizada en un gran número de sectores industriales para control de calidad de producto procesado, en busca de discontinuidades macroscópicas y defectos en su estructura interna.
En el caso de soportes cerámicos compactados, el valor y la distribución de la porosidad determina, en gran medida, las propiedades del producto final (dimensiones, curvatura, resistencia a la helada, resistencia mecánica, presencia de corazón negro, acabado superficial, etc.). Este hecho hace imprescindible realizar un control exhaustivo de la porosidad de los soportes durante su conformado, con el fin de asegurar el buen desarrollo del resto del proceso y mantener las propiedades del producto final dentro de los márgenes de variación preestablecidos, de forma que el porcentaje de bajas de producción, o de producción que no es de primera calidad, sea el menor posible.
Ante la dificultad que supondría realizar medidas directas de la porosidad de las piezas cerámicas, en la práctica industrial, la magnitud física realmente controlada es la densidad aparente de los soportes crudos. Tradicionalmente, para realizar estas medidas en planta industrial, se han utilizado metodologías diferentes a la absorción de rayos X, como el método de la inmersión en mercurio, o la reproducción del volumen mediante láser o membranas de vacío, y posterior pesaje. Estas metodologías tradicionales requieren un tiempo largo de ensayo y ofrecen una información parcial de la pieza, lo que dificulta al técnico en su labor de control y ajuste óptimo del proceso.
Desarrollo de una aplicación industrial
En el año 2014 se inició el uso de la tecnología de absorción por rayos X en planta industrial para el control de la compactación en piezas industriales, gracias a un desarrollo de equipo basado en varias patentes del Instituto de Tecnología Cerámica de Castellón (ITC-AICE).
El uso de los rayos X en este ámbito, ha permitido dar un gran paso en este proceso, debido a que, en tan sólo unos minutos, es posible medir el 100% de la superficie de la pieza, con más de 1.000 puntos de medida por centímetro cuadrado y reduciendo el tiempo de ensayo hasta en un 90%.
Los resultados que ofrece este tipo de ensayos son tres mapas 2D, representativos cada uno de ellos de la distribución de densidad aparente (kg/m3), espesor (mm) y carga (kg/m2) de la pieza inspeccionada. Un software de tratamiento adecuado para esta información aporta diferentes tipos de informes.
Figura 1. Distribución completa de densidad aparente, espesor y carga de una pieza de 60×120 cm (tiempo de ensayo: 4 min).
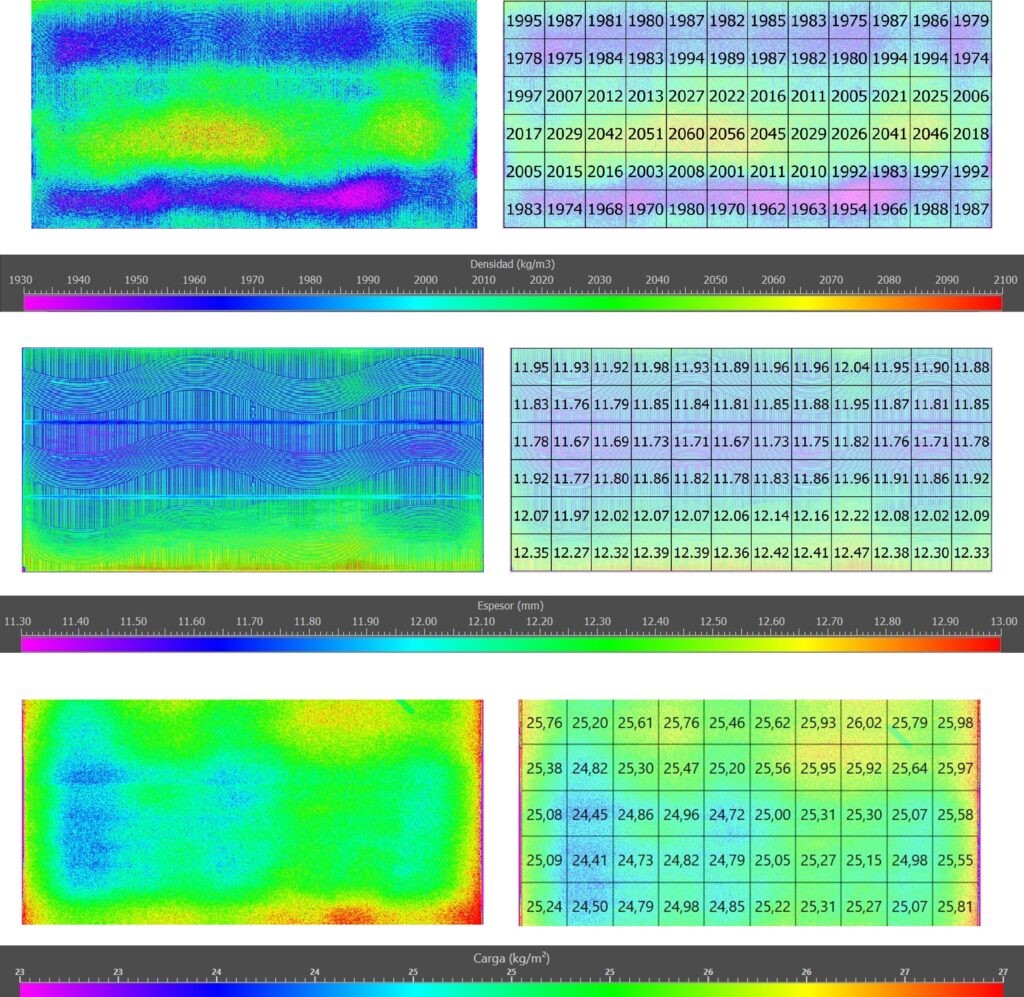
Según el diseño del equipo de medida, la pieza a medir se sitúa sobre una banda que la va transportando hacia la zona de medida de forma discontinua, paso a paso. A su vez, un tubo emisor de rayos X se desplaza transversalmente en la pieza, escaneandola de izquierda a derecha y viceversa. En el otro lado del tubo emisor se ubica un sensor de radiación, que mide la cantidad de radiación que atraviesa la pieza. Un sistema de telemetría láser acompaña también al tubo realizando la medida de espesor.
Figura 2. Perfil del equipo de medida por absorción de rayos X y telemetría láser.
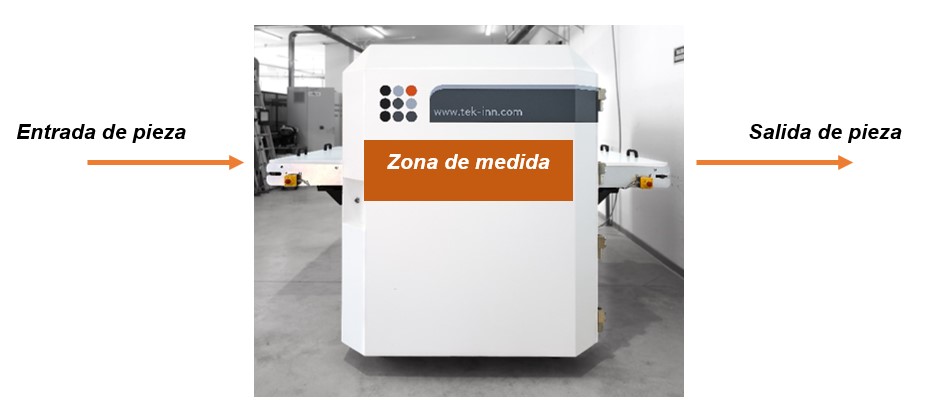
Además de la medida en pieza cruda, es posible también medir la pieza cocida. La posibilidad de caracterizar las mismas piezas, antes y después de la cocción, permite discernir si un determinado defecto es debido a un incorrecto desarrollo de la operación de prensado o, por el contrario, aparece como consecuencia de una regulación del horno no optimizada. El control mediante rayos X en el proceso de cocción también proporciona una manera rápida, aunque indirecta, de verificar si la absorción de agua en la pieza cerámica se mantiene constante.
Ventajas del uso de la tecnología de rayos X en el control de calidad de la fabricación de baldosas cerámicas
Gracias al empleo de rayos X en la etapa de prensado para medida de la compactación, el técnico dispone de una gran cantidad de información en un tiempo muy reducido. Estas variables, para cualquier proceso productivo (información y tiempo), son clave para poder tener un mayor control y certeza sobre la fabricación. De especial importancia es verificar en las etapas iniciales, como es el conformado de la pieza, ya que, como hemos visto, de una buena compactación depende que posteriormente no aparezcan problemas relacionados con el esmaltado, decoración o cocción.
Los mapas de distribución de densidad, espesor y masa obtenidos, ayudan al técnico en gran medida para el ajuste de las variables de prensado, y a la comprensión de cómo estos ajustes afectan a los cambios en la pieza, anticipando de forma ágil y efectiva la corrección de futuros fallos en la producción. Estas ventajas consiguen que la fábrica reduzca su porcentaje de mermas, y que aumente el porcentaje de primera calidad, lo que en definitiva es un importante beneficio económico al final del año.
El uso de esta tecnología está consolidada y validada en las empresas de fabricación de baldosas cerámicas, con más de 45 equipos activos en diferentes clientes productores de todo el mundo. No cabe duda de que, por las grandes ventajas que está aportando, la aplicación de verificaación de la compactación mediante rayos X seguirá extendiéndose cada vez más en el sector a nivel mundial.
